"*" indicates required fields
PM Sweet: RFID tracks millions of macarons
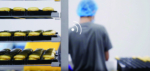
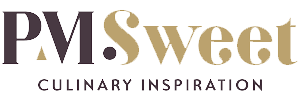
The client
PM Sweet specialises in the production of high-quality macarons. The Belgian company, with production sites in Vivegnis and Dison, has seen impressive growth, starting from artisanal experiments in the founder’s kitchen to a fully automated production process that upholds the highest quality standards. With a dedicated team of 350 employees and a modern 17,000m2 facility, PM Sweet now produces over 1,000,000 macarons per day. Their products are currently distributed in more than 30 countries.
The challenge
Effectively managing the inventory of unwrapped macarons requires precise tracking of essential information, including batch numbers, production dates and time spent in refrigeration. This is crucial for food safety, given the limited time allowed between the creation of the macarons and the moment they are packaged. PM Sweet looked for a solution to precisely and automatically capture and digitally monitor this vital data, eliminating the need for manual monitoring.
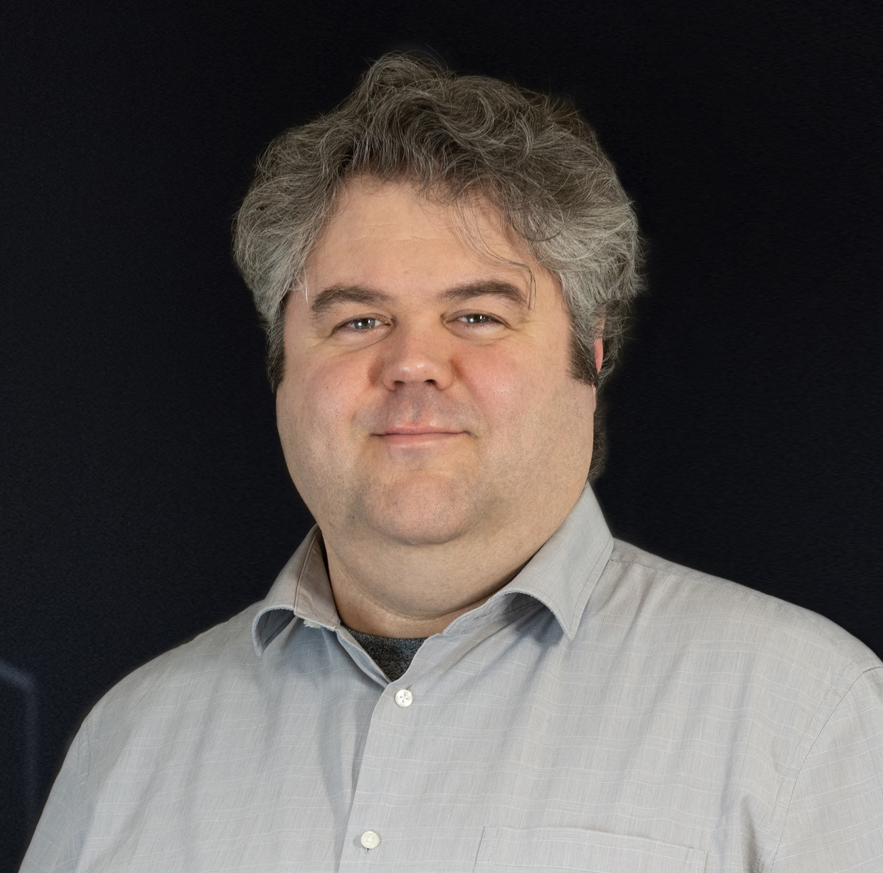
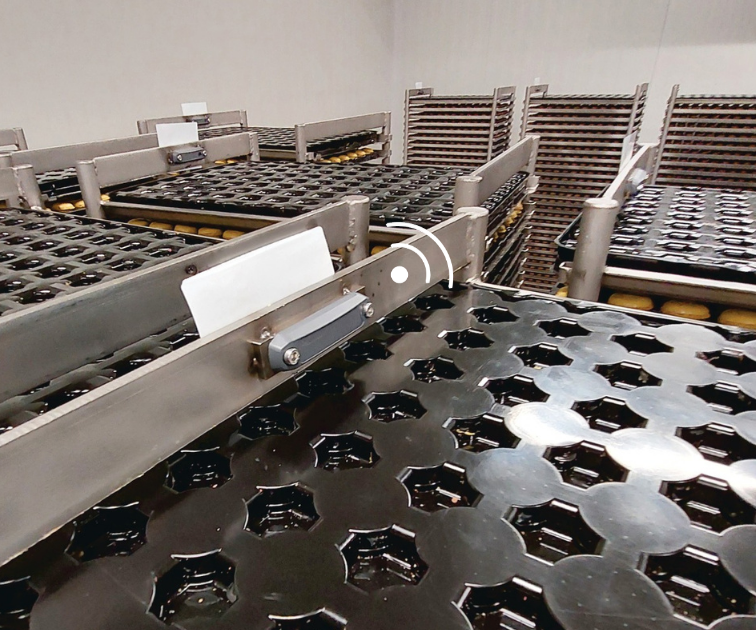
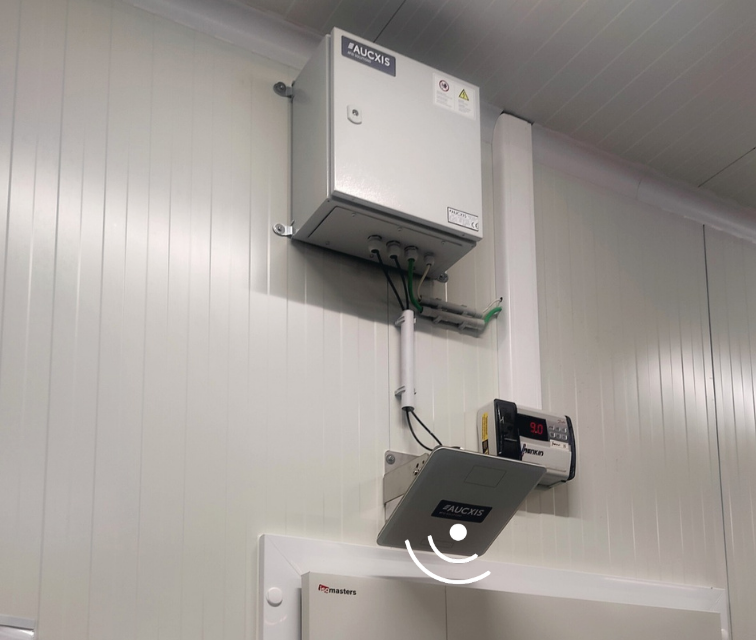
The solution
Trays with baked macarons are loaded onto a cart, transported to the fridge, and after the cooling period, brought to the packaging area. They then return to the replenishment zone. The tracking of the carts and their loads was digitised and optimised using RFID asset tracking as follows:
Each cart was equipped with a permanent UHF on-metal RFID tag and a QR code, both containing the cart’s unique identity. When a cart is loaded, a self-adhesive label with a QR code is applied, which contains information about the load. The QR codes are then scanned using a handheld device. Through the POLARIS Asset Management Software app, the cart and batch are linked, and the number of trays in the cart is added.
To track the carts, RFID antennas and RFID readers were installed at various locations. At the fridges, these were placed on each side of the entrance and exit doors. When a cart enters or exits a fridge, both its location and direction of movement are detected.
In the passage from the packaging zone to the replenishment area, RFID antennas detect the RFID tag of the empty cart, after which the cart’s contents are automatically reset.
Additional manual scans can be taken using the POLARIS app on the handheld device. This can be used, for example, to perform an inventory count in a specific area or to move carts to a zone where no antennas are present.
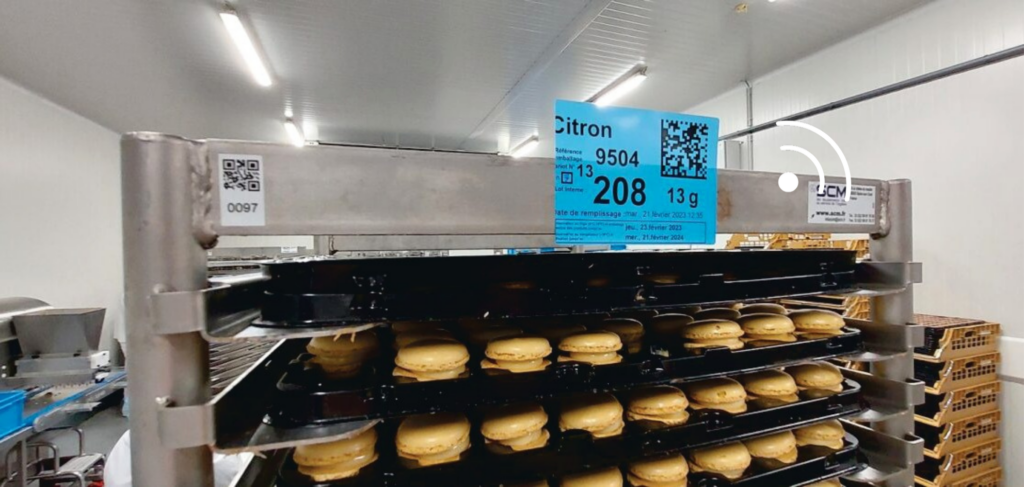
The result
- Accurate, real-time information
PM Sweet remains informed about inventory availability and its location at all times. - Time savings
Automation has eliminated time- consuming manual recordings. - Digital traceability
Key production data of the batches is 100% accurate and digitally available (batch numbers, production dates, and time spent in refrigeration), providing crucial information for food safety. - Insight into the process
Carts and their loads are precisely detected and tracked throughout the entire process, offering insights into the efficiency of the logistics process.
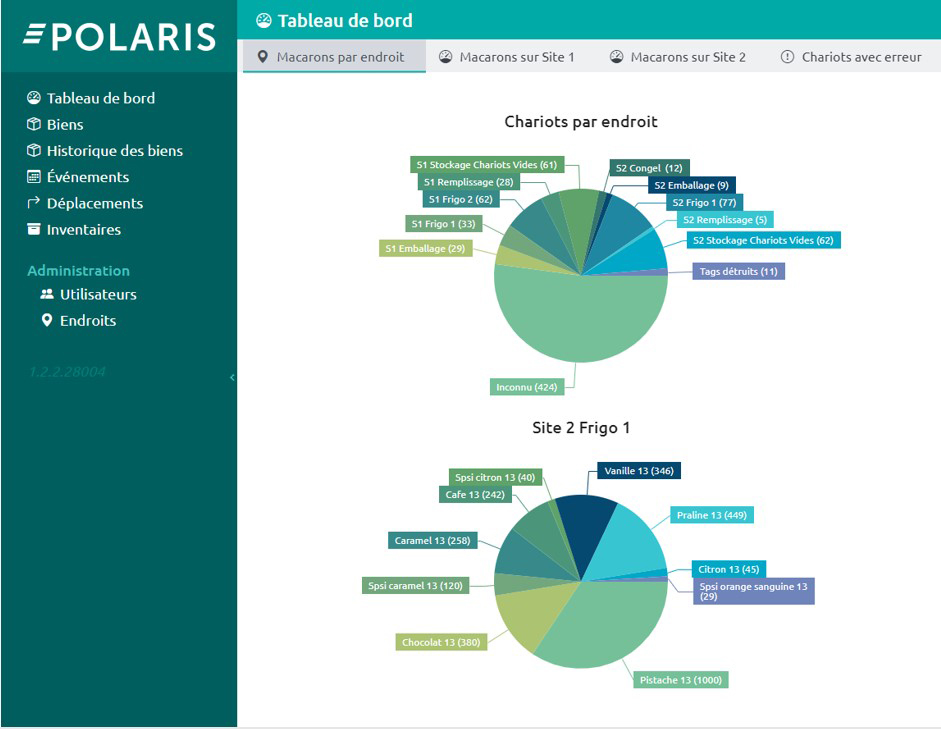
An RFID system tailored to your needs
Our modular approach allows to elaborate a solution for you which perfectly meets your needs.
Nothing more, nothing less.