"*" indicates required fields
Aertssen Logistics: automation of logistic processes with RFID
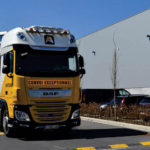

The customer
Aertssen Logistics is an expert in transport and logistics of various types of machines, from agricultural machinery, to cherry pickers such as scissor lifts and telescopic cherry pickers with tracks, to consolidation. In its distribution centre near the port of Antwerp they process every year 10.000 cherry pickers/machines for various customers.
The challenge
The pen and paper inventory was an intensive and error-prone task for Aertssen Logistics: not only because of the large number of assets to be processed, but also because certain types of machines are very similar. That is the reason why Aertssen Logistics was looking for a system enabling the automation of its logistic processes.
It quickly became clear that RFID would be the most appropriate technology to manage the stock in a faster, more accurate way and to accurately handle the delivery of machines.
The solution
Aucxis implemented the RFID Asset Management solution with the following building blocks:
- Hardware: RFID labels, RFID hand scanners and RFID outdoor gates;
- HERTZ RFID middleware for the communication between the hardware and the applications;
- POLARIS RFID software: web portal and app for the handhelds
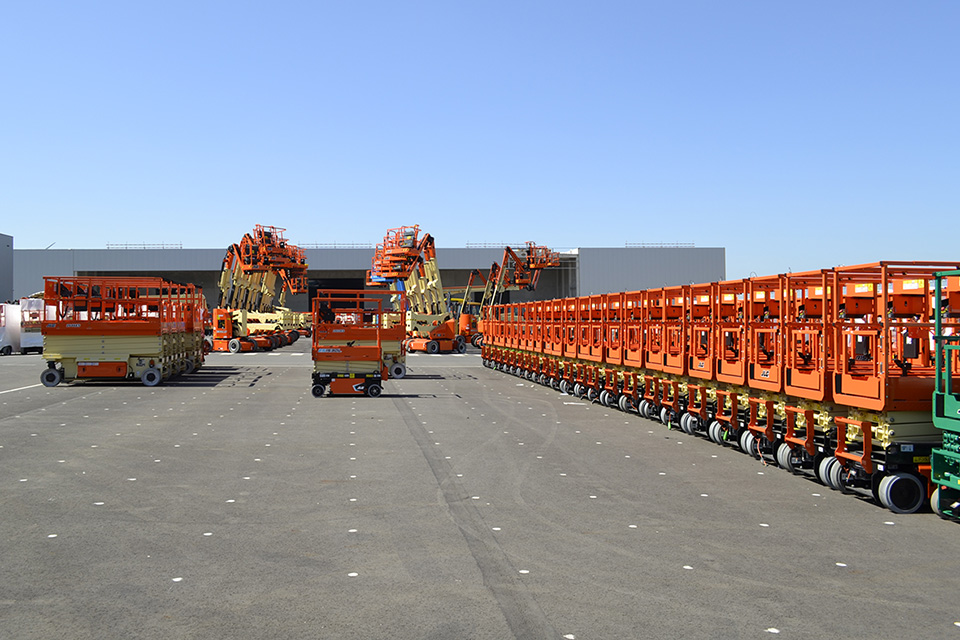
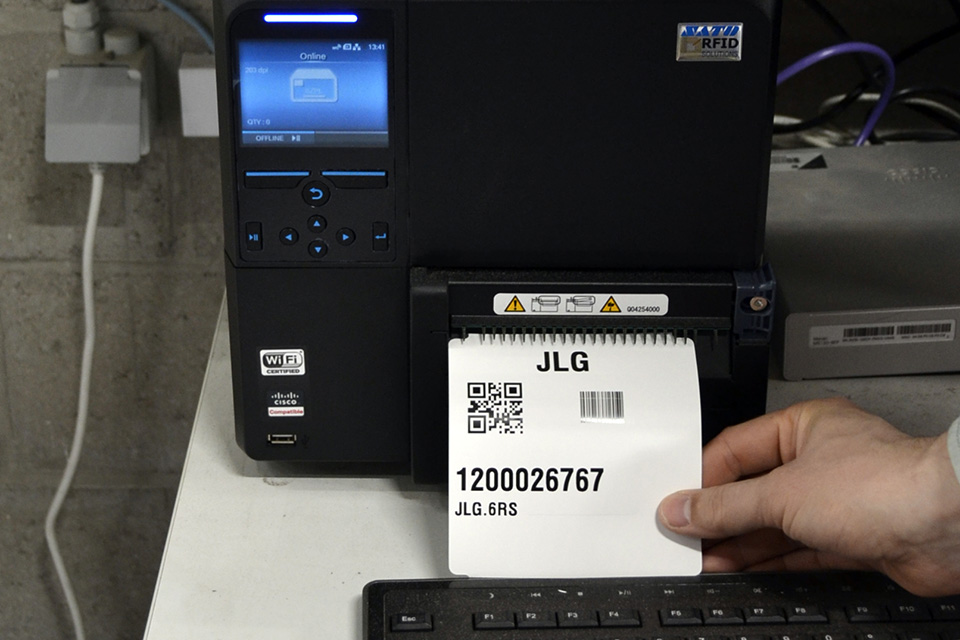
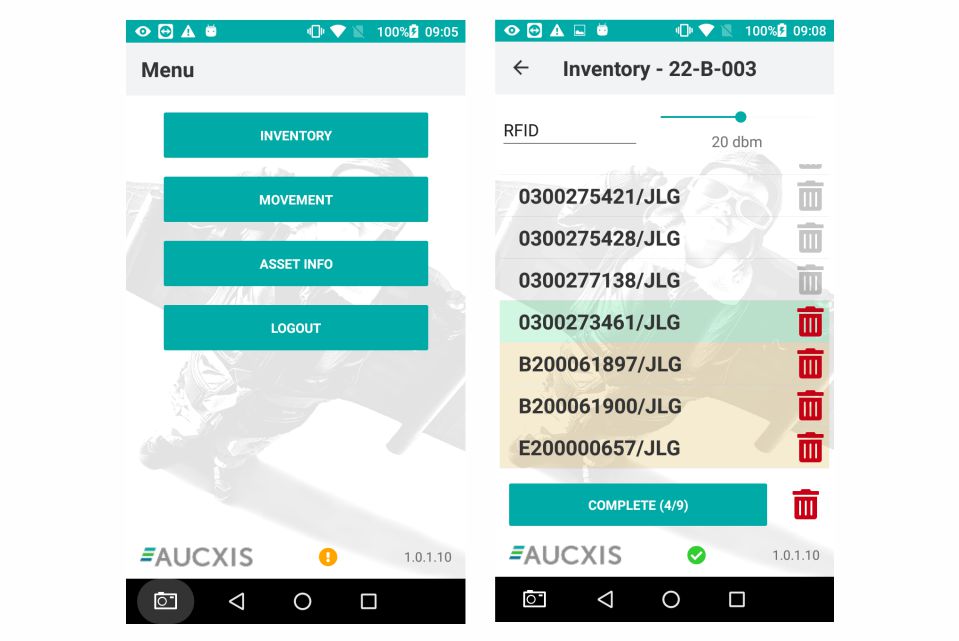
Phase 1: Manual registration, inventory and localisation at the yard
Upon arrival of the machines at Aertssen Logistics’ site, the ERP system instructs the RFID printer to print for each machine an RFID label containing product information and a QR code. All registered data are saved, managed and followed in the POLARIS software. Via filtering, the user quickly retrieves the desired information in the historical overview.
Phase 2: Registration of outgoing movements through RFID outdoor gates
Aucxis provided two waterproof and weather-resistant RFID outdoor gates for proof of shipment:
- Fixed RFID gate: for the registration of passages of loaded trucks;
- Mobile RFID gate: for the registration of passages when loading sea containers;
- Alarm in case of exit of materials which may not leave the site
The result
- Accurate and quick stock inventory;
- Gain of time of 50% thanks to the automatic detection and control upon loading: a loading list is finished considerably faster;
- Increased accuracy by using RFID outdoor gates before departure. No secondary deliveries with expensive, time-consuming corrections, and in turn satisfied customers;
- Seamless integration with Aertssen’s systems.
Watch the case video below
“RFID helps us to localise and make an inventory of the stored machines, with time savings of 50%.”
Wouter Clissen, Logistics Manager
An RFID system customised to your needs
Our modular approach allows to elaborate a solution for you which perfectly meets your needs. Nothing more, nothing less.